Electric Boost Systems
Controllable heat when and where you need it.
FIC’s unique Distributed Boost, the only intelligent way to ensure totally efficient heat distribution, comes from the company now acknowledged to be the world’s leading technical innovator in the glass industry with more experience of boosting the highly sensitive float furnaces than any other company world-wide.
A radical advance on the thermal barrier, the ultimate in efficiency is achieved by reinforcing the natural thermal convection currents in the furnace and dissipating heat where it is most needed: underneath the blanket.
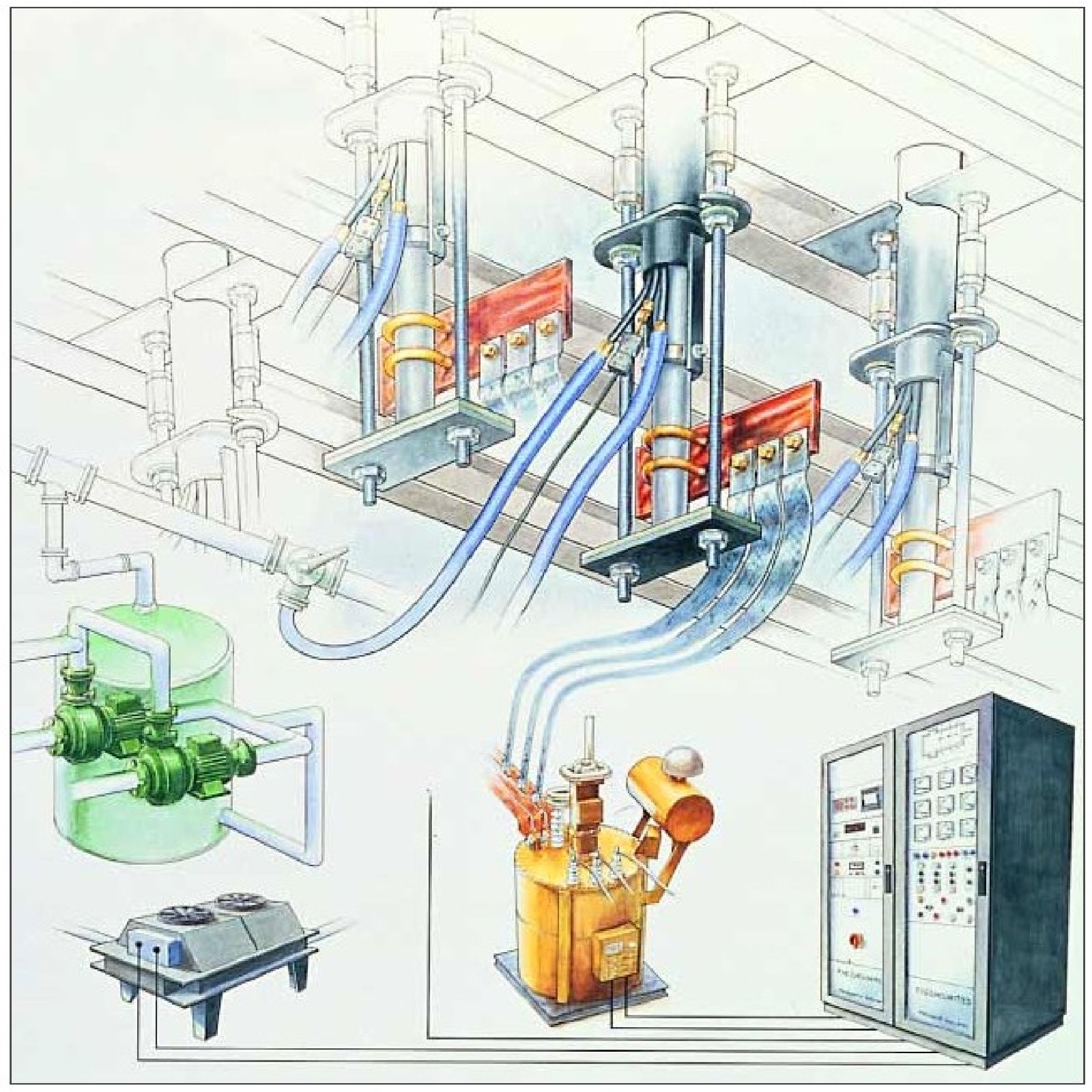
Why Boost?
Flexibility allows immediate response to market forces: extra glass over and above the furnace design capability when you need it.
Additional glass for little capital outlay.
Quality is maintained or often improved when demand is increased.
Maintained quality when melting coloured glass. The lower transmission of coloured glasses often results in lower quality. Boost eliminates this problem and is frequently used to improve existing glass quality in any colour.
Allows response to changing energy source prices and availability.
Buys time until furnace repair can be carried out.
Why FIC?
- FIC’s experience of boosting float furnaces is more extensive than that of any other company internationally. This puts it in a unique position to create the optimum method of heat distribution.
- FIC’s Distributed Boost systems have been applied to all areas of the glass industry including float, container, fibre, borosilicate and T.V. panel.
- FIC’s unique mathematical modelling ensures customized design with a far greater degree of accuracy than previously ever obtained.
- FIC’s ancillary hardware is some of the most advanced and well-proven in the industry.
- FIC has boosted more float furnaces for major glass producers than have companies such as Pilkington and St. Gobain, in-house.
- FIC has over 200 experts world-wide on whose expertise and experience it can draw.
The FIC Distributed Boost
Although some in the glass industry have favoured almost all the input at the glass hot-spot during melting, via so-called ‘barrier’ boost systems, it is generally accepted that for more efficient, cost-effective glass production of high quality the input should ‘boost’ power in a ratio of about 30/70, melt-end to hot-spot.
As FIC found in its extensive project management in the area of float furnaces, excessive localised energy released at the hot-spot simply produces a higher surface glass temperature which results in a reduced rate of heat transfer from the radiant source. This requires a reduction in fossil fuel input if limiting values for superstructure temperature are not to be exceeded. The net effect is therefore the replacement of low-cost gas by higher cost electricity.
FIC’s Distributed Boost system releases diffuse energy over the whole of the melt area.
It is now standard in the industry and has been employed by a host of clients for diverse reasons such as: the need for additional demand, capacity flexibility, other colour flexibility, shorter transition times, emission reductions, thin film production, quality improvement and campaign extension.
The Boost is also a great stand-by in times of trouble: should a furnace’s regenerative chambers become blocked, the efficiency of heat recovery drops and fuel consumption goes up. The lost energy can be recovered with a boost system which can be installed ‘hot’ and on the run.
Time can thus be bought to prepare for a proper repair and output maintained.
F.I.C. (UK) Ltd. has extensive experience of supplying boost systems to major glass producers all over the world and offers a complete service of design through to manufacture and supply, onsite installation and commissioning services.
Equipment of the very highest quality, conforming to ISO 9001, is manufactured at our modern, purpose-built premises in Penzance, Cornwall, England.
Ensuring that the precise needs of the client are met
Mathematical Modelling, well-proven and accurate to better than 1%, allows FIC to investigate and determine the most expedient and cost-efficient design based on the client’s specific requirements and hardware that he already possesses. For example, existing transformer parameters can be incorporated into a hypothesis to see if that transformer can be utilised in a boost system to save them money.
FIC’s unique Mathematical Modelling techniques help determine what are the most important design features: transformer characteristics, voltage and current range, will ensure that the client does not ultimately pay for design inefficiencies. Inaccuracy in determination of the resistivity of the glass, and consequently transformer characteristics, could result in the client not being able to achieve his objectives. A mathematical hypothesis will also determine the most effective placement of electrodes.
FIC can also provide Thermal Barrier Boosting Systems where the client has specific needs that require a different approach.
FIC offers unique software packages relating specifically to Boost.
FIC can also undertake full Mathematical Modelling of the complete furnace process including glass convection current flows and the effect of flames and batch cover.
Further Information:
-
-
Please contact us to receive more information, our latest presentation, or a quotation to purchase.